Industria 4.0: Come affrontare le sfide e le opportunità del futuro tecnologico
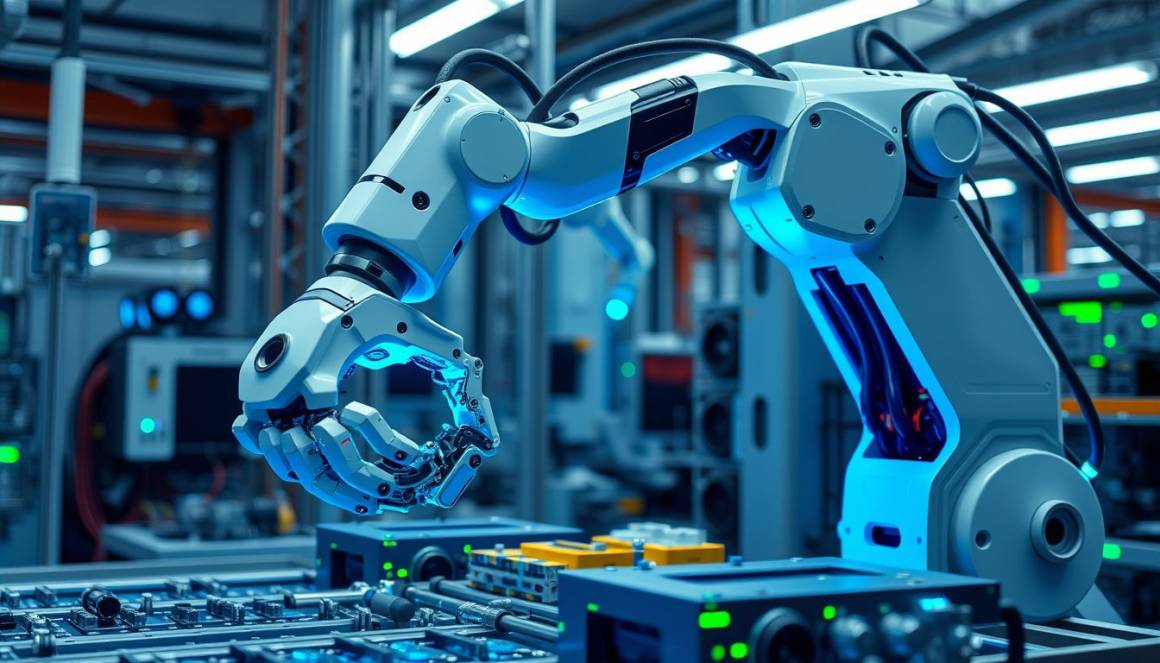
Che cos’è l’Industria 4.0: il significato e le caratteristiche
Industria 4.0: il significato e le caratteristiche
L’Industria 4.0 rappresenta un paradigma di trasformazione radicale dei processi produttivi, creando un ecosistema integrato dove le tecnologie digitali e le macchine hanno un ruolo preponderante. Questa quarta rivoluzione industriale è caratterizzata da un livello d’automazione e interconnessione mai visto prima, che ottimizza l’efficienza operativa delle aziende.
Indice dei Contenuti:
Al centro di questo cambiamento vi è l’uso intensivo di dati e delle nuove tecnologie digitali, fondamentali per lo sviluppo del manufacturing moderno. Quattro sono le direttrici principali che guidano questa evoluzione. La prima è l’aggregazione e l’elaborazione dei dati, attraverso strumenti come il big data, l’Internet of Things (IoT), il machine-to-machine communication e il cloud computing. Trattare grandi volumi di dati permette alle aziende non solo di centralizzare le informazioni, ma anche di migliorarne la qualità e l’accessibilità.
La seconda direttrice si concentra sull’analisi dei dati, o “analytics”. Non basta raccogliere dati: le aziende devono estrarne valore. Attualmente, si stima che solo l’1% dei dati raccolti venga sfruttato. Con l’adozione di tecniche di machine learning, le aziende possono ottimizzare le loro operazioni e migliorare i processi decisionali basandosi sull’analisi predittiva.
La terza direttrice si riferisce alla crescente interazione tra esseri umani e macchine, attraverso interfacce intelligenti come i sistemi touch, la realtà aumentata e le tecnologie di interazione avanzata. Questo avvicinamento porta a un lavoro più collaborativo, in cui le competenze umane vengono abbinate alla potenza delle macchine per raggiungere risultati superiori.
L’ultima direttrice tocca l’integrazione e il passaggio dal digitale al mondo reale, settore dove appaiono significativi progressi con l’adozione della manifattura additiva, della stampa 3D e dell’uso di robot e automazioni avanzate. Questa convergenza di tecnologie permette di razionalizzare i costi e migliorare l’efficienza delle risorse nella produzione, esaltando la flessibilità e la sostenibilità delle attività industriali.
Come nasce il termine Industria 4.0
L’appellativo “Industria 4.0” ha fatto il suo debutto nel 2011, in occasione della Fiera di Hannover, in Germania. Questa esposizione internazionale ha rappresentato un momento cruciale per l’industrializzazione contemporanea, permettendo di abbozzare una visione chiara della trasformazione in atto. A seguito di questo evento, nel 2012 è stato costituito un gruppo di lavoro su Industrie 4.0, diretto da figure chiave quali Siegfried Dais, di Robert Bosch GmbH, e Henning Kagermann, dell’Accademia tedesca delle scienze e dell’ingegneria (Acatech). Questo gruppo ha formulato raccomandazioni strategiche per l’implementazione della nuova era industriale, sottolineando l’importanza di un approccio integrato e innovativo nell’industria.
Il rapporto finale del gruppo, presentato all’attenzione del governo federale tedesco nell’aprile 2013, ha gettato le basi per una serie di politiche volte a incoraggiare le aziende a investire e adottare tecnologie avanzate. Il termine stessa di “Industria 4.0” si riferisce, quindi, non solo a un insieme di tecnologie, ma a un movimento culturale e strutturale destinato a modernizzare i processi produttivi attraverso l’adozione di sistemi smart e interconnessi.
Ma come si inquadra questo concetto nello sviluppo delle precedenti rivoluzioni industriali? Fino adesso, la storia ha registrato tre trasformazioni significative: la prima con l’introduzione della macchina a vapore, la seconda con l’elettrificazione e la produzione di massa, e la terza con la digitalizzazione e l’uso dell’informatica. La quarta rivoluzione rappresenta una fusione tra il mondo fisico e quello digitale, grazie all’industrial internet e alla digitalizzazione dei processi produttivi.
Dunque, l’emergere di Industrie 4.0 non è casuale; è frutto di una necessità sempre crescente di efficienza, capacità di innovazione e sostenibilità nel panorama globale. Ciò implica non solo l’integrazione di tecnologie avanzate, ma anche un ripensamento delle modalità organizzative e lavorative nelle fabbriche, così come delle competenze richieste. In questo modo, l’Industria 4.0 si configura come un volano per incrementare la competitività delle aziende in un contesto economico in continua evoluzione.
Tecnologie e innovazioni dell’Industria 4.0
L’Industria 4.0 si fonda su un insieme di tecnologie innovative che trasformano radicalmente il panorama produttivo e operativo delle aziende. Il concetto di smart manufacturing è supportato da alcuni elementi chiave, definiti dall’Osservatorio Industria 4.0 del Politecnico di Milano, che identificano quale sia il vero motore di questa evoluzione. Tra le tecnologie principali si annoverano il Manufacturing Big Data, la Additive Manufacturing (o stampa 3D), l’Industrial Internet of Things, il Cloud, l’Advanced Automation e le interfacce uomo-macchina avanzate, note come Advanced HMI.
La prima tecnologia, il Manufacturing Big Data, si riferisce alla raccolta, analisi e utilizzo avanzato dei dati generati durante i processi produttivi. L’analisi dei big data consente di ottimizzare le operazioni, prevedere eventi critici e migliorare la qualità del prodotto finale, un aspetto cruciale in un’era dove la personalizzazione e l’efficienza sono fondamentali.
L’Additive Manufacturing gioca un ruolo centrale nella produzione 4.0, in quanto permette di fabbricare componenti in modo più flessibile e veloce, riducendo gli sprechi e il tempo di produzione. Attraverso la stampa 3D, le aziende possono realizzare prototipi e produzioni su richiesta, rendendo il processo estremamente adattabile alle esigenze del mercato.
Essenziale per l’interconnessione delle macchine è l’Industrial Internet of Things, una rete di dispositivi intelligenti e sensori capace di raccogliere e condividere dati in tempo reale. Questo permette non solo un monitoraggio continuo ma anche un’ottimizzazione costante dei processi nelle catene di produzione.
Il Cloud rappresenta l’infrastruttura abilitante per il trattamento e la conservazione dei dati, garantendo accessibilità e scalabilità alle imprese. Permette di archiviare enormi quantità di informazioni e fornire strumenti di analisi avanzati, fondamentali per supportare decisioni strategiche.
Infine, l’Advanced Automation e le Advanced HMI favoriscono l’interazione sicura e intuitiva tra operatori e macchine. Attraverso interfacce più intuitive, gli operatori possono controllare facilmente i processi, mentre la robotica avanzata offre possibilità di automazione precedentemente inimmaginabili, aumentando la produttività e riducendo gli errori.
L’integrazione di queste tecnologie innovativa è cruciale per realizzare il potenziale dell’Industria 4.0, permettendo alle aziende di diventare più agili, reattive e competitive in un ambiente globale sempre più complesso e dinamico.
Come l’Industria 4.0 cambia le fabbriche e i processi produttivi
Nella nuova era dell’Industria 4.0, assistiamo a una trasformazione radicale delle fabbriche e dei processi produttivi. Le aziende non si limitano più a ottimizzare le operazioni, ma si stanno ripensando in termini di struttura e di interconnessione tra tutti gli elementi coinvolti. Al centro di questo cambiamento ci sono macchine e sistemi che non solo comunicano tra loro, ma imparano, si adattano e migliorano continuamente la propria efficienza attraverso l’analisi dei dati.
La Fabbrica 4.0 costituisce un ecosistema dove le tecnologie digitali e fisiche si fondono, dando vita a sistemi completamente interconnessi. L’Internet delle Cose (IoT) richiede impianti connessi tra loro, consentendo il monitoraggio in tempo reale delle performance e una programmazione predittiva della manutenzione. Grazie a questo approccio, le macchine possono eseguire autodiagnosi, ottimizzando la loro operatività e prevenendo fermi macchina indesiderati.
Uno degli aspetti più significativi è la capacità di personalizzazione dei prodotti. Le nuove tecnologie, come la manifattura additiva e le linee di produzione modulari, rendono possibile modificare i processi produttivi per rispondere a specifiche richieste del cliente, aumentando così la flessibilità. Le aziende possono passare da produzioni di massa a produzioni personalizzate senza dover effettuare investimenti insostenibili o rallentare il processo produttivo.
La gestione delle risorse è un altro punto focale del cambiamento. Grazie alla digitalizzazione, le fabbriche possono gestire i flussi energetici in maniera più razionale, riducendo gli sprechi e ottimizzando i costi. Le tecnologie di analisi avanzata possono identificare aree di inefficienza, fornendo soluzioni tempestive e permettendo di realizzare operazioni più sostenibili dal punto di vista ambiente.
L’Industria 4.0 favorisce anche un nuovo modello di interazione tra l’uomo e la macchina. Le interfacce naturali, come la realtà aumentata e i sistemi di realtà virtuale, stanno cambiando il modo in cui gli operatori interagiscono con le macchine. Non più semplici esecutori, gli operatori diventano parte attiva del processo, utilizzando le loro competenze in sinergia con le tecnologie avanzate, ottimizzando così il risultato finale.
L’importanza delle competenze digitali nell’Industria 4.0
Nel contesto della quarta rivoluzione industriale, le competenze digitali emergono come un elemento cruciale per il successo delle aziende. La transizione verso l’Industria 4.0 richiede una forza lavoro altamente qualificata, capace di affrontare sfide innovative e di adattarsi a un ambiente in costante cambiamento. Tuttavia, le aziende italiane si trovano frequentemente a dover fare i conti con una realtà preoccupante: la difficoltà di trovare professionisti con le competenze adatte per sfruttare a pieno le opportunità offerte da questa nuova era.
Le competenze digitali si riferiscono a un ampio ventaglio di abilità che abilitano i lavoratori a usare le tecnologie informatiche in vari ambiti, dal controllo dei processi produttivi all’analisi dei dati. È fondamentale che il sistema educativo, dalle scuole superiori alle università, si adatti a soddisfare questa domanda di competenze. Le istituzioni formative devono sviluppare percorsi didattici che non solo trasmettano conoscenze teoriche, ma anche abilità pratiche, per preparare i giovani ad integrarsi efficacemente nel mondo del lavoro.
Il Piano Nazionale Industria 4.0, avviato nel 2016, destina risorse significative per incentivare la formazione del personale, con misure come il credito d’imposta per la formazione 4.0 e il voucher per l’Innovation manager. Tuttavia, è chiaro che c’è ancora molto da fare. Gli istituti tecnici e i licei, in particolare, dovrebbero sclpire una specializzazione maggiore nel fornire competenze digitali certificate, che possano realmente facilitare l’occupazione dei neolaureati.
Le aziende stesse sono invitate a investire nella formazione continua del proprio personale. Investire nelle competenze digitali non solo aiuta a anticipare le necessità del mercato, ma offre anche un vantaggio competitivo decisivo in una economia sempre più basata sulla tecnologia. I dipendenti con competenze digitali elevate possono collaborare efficacemente con le tecnologie avanzate, facilitando la transizione verso pratiche più sostenibili e innovative.
Il futuro dell’Industria 4.0 non può prescindere dall’impegno collettivo a creare un ecosistema in cui formazione e innovazione si alimentano reciprocamente. È indispensabile che aziende, scuole e istituzioni pubbliche collaborino per sviluppare un piano ben definito per la formazione digitale, promuovendo attività di aggiornamento e certificazione che possano sostenere la crescita professionale. Solo così si potrà garantire una forza lavoro pronta a rispondere alle sfide innovative e competitive dell’era 4.0.
Sostieni Assodigitale.it nella sua opera di divulgazione
Grazie per avere selezionato e letto questo articolo che ti offriamo per sempre gratuitamente, senza invasivi banner pubblicitari o imbarazzanti paywall e se ritieni che questo articolo per te abbia rappresentato un arricchimento personale e culturale puoi finanziare il nostro lavoro con un piccolo sostegno di 1 chf semplicemente CLICCANDO QUI.